High Pressure Die Casting
Precise Analysis Considering
Actual Vacuum Conditions
What we can simulate in the
High Pressure Die Casting process
High Pressure Die Casting
GAS
Gas Porosity Defects

Gas Defect Occurrence During & After Filling
Gas pressure is predicted by calculating the pressure of the melt & pressure in the air. Gas amount quantitatively predicts gas amount and isolation along with the gas amount in the melt. During filling, oxide can be tracked to predict the final isolated area, and leak defects can be predicted by considering shrinkage defects, machining areas and water/oil paths in the product.



High Pressure Die Casting
Shot Sleeve
Analysis of Shot Speed
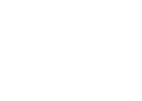
Optimized Shot Sleeve
In the high pressure die casting process, the sleeve condition settings are the most basic procedure. Various types of defects occurring during filling can be predicted according to the low and high speed condition within the sleeve.



High Pressure Die Casting
Vacuum
Analysis of Vacuum Die Casting
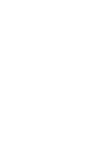
Realistic Vacuum Equipment Conditions
Based on the equipment settings, the user can easily check the pressure history by observing the pressure loss during vacuum use and the actual pressure graph applied to the product. By observing the actual pressure applied in the cavity, the user can optimize the vacuum equipment selection and apply it to real life.



High Pressure Die Casting
Die Life
Predict of Die Damages

Defects affecting Die Life
It is possible to increase die life and to derive casting conditions through prediction of soldering defects calculated by considering the surface treatment of the mold and product ejection time, along with the prediction of mold erosion defects caused by the speed, temperature of melt and shape of the mold during filling.



High Pressure Die Casting
Deformation
Prediction of
Deformation and Crack
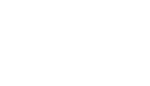
Predict Various Defects Caused by Deformation
Based on the temperature distribution result data, the deformation and cracking of the product can be predicted through mapping work using FEM mesh, and the effect of reducing shrinkage defects can be verified by using local squeeze pins when solidification occurs in a specific area of the product. In addition, it is possible to derive a safe eject pin position by predicting the safety factor of the mentioned eject pin.



High Pressure Die Casting
Shrinkage
Prediction of Micro & Macro
Shrinkage Defect
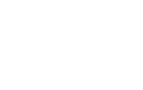
Analysis of Shrinkage from Solidification Pattern & Gas
The area of residual melt isolated during solidification is tracked to predict areas with high possibility of macro shrinkage defects based on the probabilistic defect model. Micro shrinkage – which are difficult to predict by tracking residual melt, can be predicted by considering the gas concentration inside the melt during solidification leading to observing the growth mechanism of gas.



High Pressure Die Casting
Cooling Channel
Analysis of Various
Cooling Channels
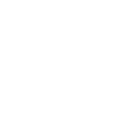
Improved Analysis Accuracy by Channel
Consideration
It is possible to maintain the temperature balance of the mold, control shrinkage defects, and minimize deformation by using cooling and constant temperature channels during solidification. For special channels such as spot channel cooling, heat transfer coefficients according to the length of the channel are set to be similar to the actual product. The user may take into account the cooling effect.



High Pressure Die Casting
Speed
Save Human Resource
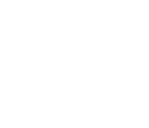
Reduce Time Consuming Work
Auto-Mesh creates meshes within 3-clicks for beginners. It detects the thickness of each area in the casting design, automatically adjusts the number of meshes, and generates meshes on the x, y, and z axis. In addition, it is possible to draft a report using the preset basic form through simple information input and observe the result like anyPOST in PowerPoint. Results Combination, which allows union and intersection combinations based on multiple results, enables various and clear result prediction.



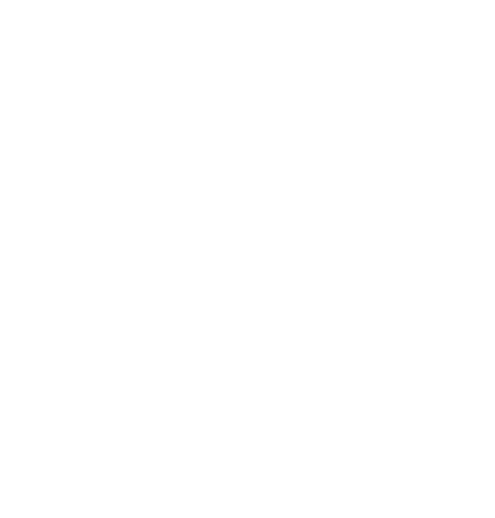
- GAS
- Gas Defect Occurrence During & After Filling
- Gas pressure is predicted by calculating the pressure of the melt & pressure in the air. Gas amount quantitatively predicts gas amount and isolation along with the gas amount in the melt. During filling, oxide can be tracked to predict the final isolated area, and leak defects can be predicted by considering shrinkage defects, machining areas and water/oil paths in the product.
- See More
- Shot Sleeve
- Optimized Shot Sleeve
- In the high pressure die casting process, the sleeve condition settings are the most basic procedure. Various types of defects occurring during filling can be predicted according to the low and high speed condition within the sleeve.
- See More
- Vacuum
- Realistic Vacuum Equipment Conditions
- Based on the equipment settings, the user can easily check the pressure history by observing the pressure loss during vacuum use and the actual pressure graph applied to the product. By observing the actual pressure applied in the cavity, the user can optimize the vacuum equipment selection and apply it to real life.
- See More
- Die Life
- Defects affecting Die Life
- It is possible to increase die life and to derive casting conditions through prediction of soldering defects calculated by considering the surface treatment of the mold and product ejection time, along with the prediction of mold erosion defects caused by the speed, temperature of melt and shape of the mold during filling.
- See More
- Deformation
- Predict Various Defects Caused by Deformation
- Based on the temperature distribution result data, the deformation and cracking of the product can be predicted through mapping work using FEM mesh, and the effect of reducing shrinkage defects can be verified by using local squeeze pins when solidification occurs in a specific area of the product. In addition, it is possible to derive a safe eject pin position by predicting the safety factor of the mentioned eject pin.
- See More
- Shrinkage
- Analysis of Shrinkage from Solidification Pattern & Gas
- The area of residual melt isolated during solidification is tracked to predict areas with high possibility of macro shrinkage defects based on the probabilistic defect model. Micro shrinkage – which are difficult to predict by tracking residual melt, can be predicted by considering the gas concentration inside the melt during solidification leading to observing the growth mechanism of gas.
- See More
- Cooling Channel
- Improved Analysis Accuracy by Channel Consideration
- It is possible to maintain the temperature balance of the mold, control shrinkage defects, and minimize deformation by using cooling and constant temperature channels during solidification. For special channels such as spot channel cooling, heat transfer coefficients according to the length of the channel are set to be similar to the actual product. The user may take into account the cooling effect.
- See More
- Speed
- Reduce Time Consuming Work
- Auto-Mesh creates meshes within 3-clicks for beginners. It detects the thickness of each area in the casting design, automatically adjusts the number of meshes, and generates meshes on the x, y, and z axis. In addition, it is possible to draft a report using the preset basic form through simple information input and observe the result like anyPOST in PowerPoint. Results Combination, which allows union and intersection combinations based on multiple results, enables various and clear result prediction.
- See More
Sand Casting
Database of Various Subsidiary
Materials used in Sand Casting
What we can simulate in the
Sand Casting process
Sand Casting
Shrinkage
Prediction of Micro & Macro
Shrinkage Defect
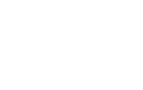
Analysis of Shrinkage from Solidification Pattern & Gas
The area of residual melt isolated during solidification is tracked to predict areas with high possibility of macro shrinkage defects based on the probabilistic defect model. Micro shrinkage – which are difficult to predict by tracking residual melt, can be predicted by considering the gas concentration inside the melt during solidification leading to observing the growth mechanism of gas.



Sand Casting
Alloy
Thermo Dynamics Calculation
of Material Properties
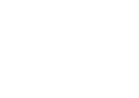
Thermal Properties Calculation
If there is no information to be used in the thermal property database within the program, the user can calculate the thermal property required for analysis by entering the chemical composition of the material. The thermal properties of a material are the most basic data in the analysis. In order to simulate accurately, the exact thermal data must be used.



Sand Casting
Cast Iron
Predict Microstructure
on Metallurgical Base
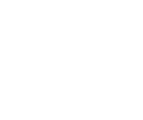
Phase Distribution & Mechanical Property
For gray cast iron and ductile cast iron, phase (Pearlite, Ferrite, Graphite, Cementite) distribution can be predicted by considering the chemical composition value of each material and mechanical properties (Tensile Strength, Yield Strength, Hardness, Elongation) can be predicted.
This function is calculation range is below the solid transformation temperature in principle.



Sand Casting
Gas
Prediction of Gas
Distribution

Core Gas Defect Before & After Filling
Gas Pressure is predicted by calculating the pressure of melt and isolated air area whereas Gas Amount predicts the movement, isolated distribution and amount of gas. It is possible to observe the movement of core gas generated from the contact in between the melt and the core along with the final isolated area. The results can then be expressed as a graph oh the amount of gas generated and discharged amount through the vent, etc.



Sand Casting
Microporosity
Shrinkage Induced
Gas Porosity (SIGAP)
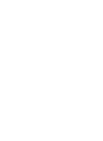
Micro Shrinkage Defects using Gas Concentration
This is a method of identifying shrinkage defect areas that are difficult to predict by the observing the retained melt during solidification, which is generally used to identify defects by predicting gas in the melt. This method considers the growth of gas bubble in the molten metal during solidification, and is a method differentiated from other micro shrinkage defect prediction techniques.



Sand Casting
Riser
Feeding Effect to Decrease
Shrinkage Defect
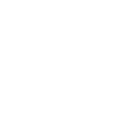
Feeding Effect on Shrinkage Defects
In order to compensate for the shrinkage defect within the cavity, a riser is placed at the area of shrinkage. In order to maximize the effect of feeding, the size is determined in consideration of the casting yield. An exothermic sleeve or powder can be used for the effect of direction solidification to reduce shrinkage.



Sand Casting
Inclusion
Find Various Inclusion Defect
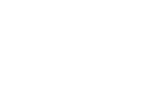
Inclusion Defects in Sand Casting
Sand drop and oxide defects are typical inclusion defects in the sand casting process. Defects caused by sand drop are dominant and through simulation, it is possible to predict the area where the melt impact during filling will affect the mold. In addition, it is possible to observe the change in the flow rate of the melt by installing a filter, so that the analysis considering the stability of the melt flow during filling is possible.



Sand Casting
Speed
Save Human Resource
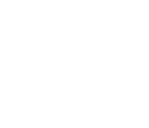
Reduce Time Consuming Work
Auto-Mesh creates meshes within 3-clicks for beginners. It detects the thickness of each area in the casting design, automatically adjusts the number of meshes, and generates meshes on the x, y, and z axis. In addition, it is possible to draft a report using the preset basic form through simple information input and observe the result like anyPOST in PowerPoint. Results Combination, which allows union and intersection combinations based on multiple results, enables various and clear result prediction.



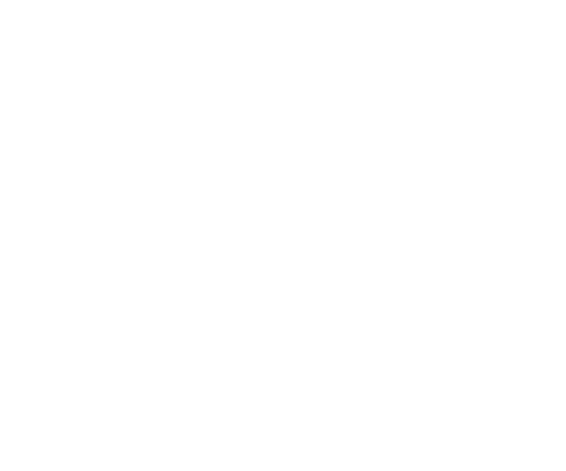
- Shrinkage
- Analysis of Shrinkage from Solidification Pattern & Gas
- The area of residual melt isolated during solidification is tracked to predict areas with high possibility of macro shrinkage defects based on the probabilistic defect model. Micro shrinkage – which are difficult to predict by tracking residual melt, can be predicted by considering the gas concentration inside the melt during solidification leading to observing the growth mechanism of gas.
- See More
- Alloy
- Thermal Properties Calculation
- If there is no information to be used in the thermal property database within the program, the user can calculate the thermal property required for analysis by entering the chemical composition of the material. The thermal properties of a material are the most basic data in the analysis. In order to simulate accurately, the exact thermal data must be used.
- See More
- Cast Iron
- Phase Distribution & Mechanical Property
- For gray cast iron and ductile cast iron, phase (Pearlite, Ferrite, Graphite, Cementite) distribution can be predicted by considering the chemical composition value of each material and mechanical properties (Tensile Strength, Yield Strength, Hardness, Elongation) can be predicted.
This function is calculation range is below the solid transformation temperature in principle. - See More
- Gas
- Core Gas Defect Before & After Filling
- Gas Pressure is predicted by calculating the pressure of melt and isolated air area whereas Gas Amount predicts the movement, isolated distribution and amount of gas. It is possible to observe the movement of core gas generated from the contact in between the melt and the core along with the final isolated area. The results can then be expressed as a graph oh the amount of gas generated and discharged amount through the vent, etc.
- See More
- Microporosity
- Micro Shrinkage Defects using Gas Concentration
- This is a method of identifying shrinkage defect areas that are difficult to predict by the observing the retained melt during solidification, which is generally used to identify defects by predicting gas in the melt. This method considers the growth of gas bubble in the molten metal during solidification, and is a method differentiated from other micro shrinkage defect prediction techniques.
- See More
- Riser
- Feeding Effect on Shrinkage Defects
- In order to compensate for the shrinkage defect within the cavity, a riser is placed at the area of shrinkage. In order to maximize the effect of feeding, the size is determined in consideration of the casting yield. An exothermic sleeve or powder can be used for the effect of direction solidification to reduce shrinkage.
- See More
- Inclusion
- Inclusion Defects in Sand Casting
- Sand drop and oxide defects are typical inclusion defects in the sand casting process. Defects caused by sand drop are dominant and through simulation, it is possible to predict the area where the melt impact during filling will affect the mold. In addition, it is possible to observe the change in the flow rate of the melt by installing a filter, so that the analysis considering the stability of the melt flow during filling is possible.
- See More
- Speed
- Reduce Time Consuming Work
- Auto-Mesh creates meshes within 3-clicks for beginners. It detects the thickness of each area in the casting design, automatically adjusts the number of meshes, and generates meshes on the x, y, and z axis. In addition, it is possible to draft a report using the preset basic form through simple information input and observe the result like anyPOST in PowerPoint. Results Combination, which allows union and intersection combinations based on multiple results, enables various and clear result prediction.
- See More
Low Pressure Die Casting
Counter Pressure Casting Analysis
Possible as well as LPDC
What we can simulate in the
Low Pressure Die Casting process
Low Pressure Die Casting
Gas
Gas Porosity Defects

Gas Defect Occurrence During & After Filling
Gas pressure is predicted by calculating the pressure of the melt & pressure in the air. Gas amount quantitatively predicts gas movement and isolation along with the gas amount in the melt. During filling, oxide can be tracked to predict the final isolated area, and leak defects can be predicted by considering shrinkage defects, machining areas and water/oil paths in the product.



Low Pressure Die Casting
Shrinkage
Prediction of Micro & Macro Shrinkage Defect
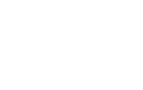
Analysis of Shrinkage from Solidification Pattern & Gas
The area of residual melt isolated during solidification is tracked to predict areas with high possibility of macro shrinkage defects based on the probabilistic defect model. Micro shrinkage – which are difficult to predict by tracking residual melt, can be predicted by considering the gas concentration inside the melt during solidification leading to observing the growth mechanism of gas.



Low Pressure Die Casting
Alloy
Thermo Dynamics Calculation of Material Properties
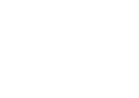
Thermal Properties Calculation
If there is no information to be used in the thermal property database within the program, the user can calculate the thermal property required for analysis by entering the chemical composition of the material. The thermal properties of a material are the most basic data in the analysis. In order to simulate accurately, the exact thermal data must be used.



Low Pressure Die Casting
Vacuum
Analysis of Vacuum
Die Casting
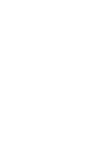
Realistic Vacuum Equipment Conditions
Based on the equipment settings, the user can easily check the pressure history by observing the pressure loss during vacuum use and the actual pressure graph applied to the product. By observing the actual pressure applied in the cavity, the user can optimize the vacuum equipment selection and apply it to real life.



Low Pressure Die Casting
Inclusion
Predict of Various Inclusions
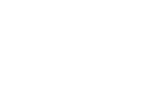
Oxide Prediction during Filling
In general, Al alloy is used in the low pressure die casting process, and due to the characteristics of Al alloy, it is vulnerable to oxidation. Oxide is formed due to air contact with the free surface of melt during filling, and there is a high probability of defects occurring in areas where the formed oxide is concentrated.



Low Pressure Die Casting
Microporosity
Prediction of Micro Shrinkage
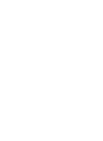
Micro Shrinkage Defects using Gas Concentration
This is a method of identifying shrinkage defect areas that are difficult to predict by the retained melt tracing method during solidification, which is a general shrinkage defect method, which is predicted by gas in the melt.
Microporosity calculations can consider external pressure. Using these points, microporosity is used when checking shrinkage defects in Counter Pressure Casting (CPC).



Low Pressure Die Casting
Cooling Channel
Analysis of Various
Cooling Channels
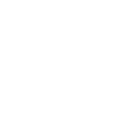
Improved Analysis Accuracy by Channel
Consideration
It is possible to maintain the temperature balance of the mold, control shrinkage defects, and minimize deformation by using cooling and constant temperature channels during solidification. For special channels such as spot channel cooling, heat transfer coefficients according to the length of the channel are set to be similar to the actual product. The user may take into account the cooling effect.



Low Pressure Die Casting
Speed
Save Human Resource
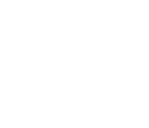
Reduce Time Consuming Work
Auto-Mesh creates meshes within 3-clicks for beginners. It detects the thickness of each area in the casting design, automatically adjusts the number of meshes, and generates meshes on the x, y, and z axis. In addition, it is possible to draft a report using the preset basic form through simple information input and observe the result like anyPOST in PowerPoint. Results Combination, which allows union and intersection combinations based on multiple results, enables various and clear result prediction.



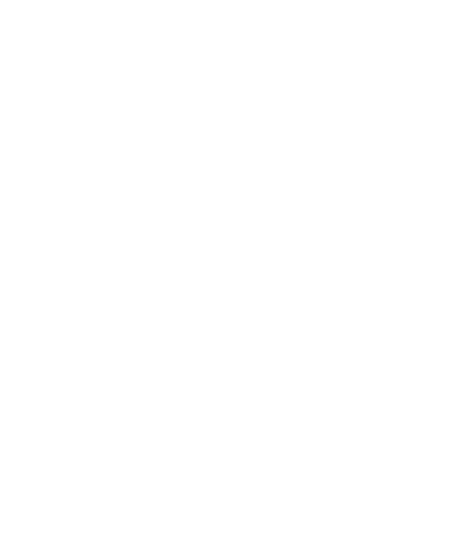
- Gas
- Gas Defect Occurrence During & After Filling
- Gas pressure is predicted by calculating the pressure of the melt & pressure in the air. Gas amount quantitatively predicts gas movement and isolation along with the gas amount in the melt. During filling, oxide can be tracked to predict the final isolated area, and leak defects can be predicted by considering shrinkage defects, machining areas and water/oil paths in the product.
- See More
- Shrinkage
- Analysis of Shrinkage from Solidification Pattern & Gas
- The area of residual melt isolated during solidification is tracked to predict areas with high possibility of macro shrinkage defects based on the probabilistic defect model. Micro shrinkage – which are difficult to predict by tracking residual melt, can be predicted by considering the gas concentration inside the melt during solidification leading to observing the growth mechanism of gas.
- See More
- Alloy
- Thermal Properties Calculation
- If there is no information to be used in the thermal property database within the program, the user can calculate the thermal property required for analysis by entering the chemical composition of the material. The thermal properties of a material are the most basic data in the analysis. In order to simulate accurately, the exact thermal data must be used.
- See More
- Vacuum
- Realistic Vacuum Equipment Conditions
- Based on the equipment settings, the user can easily check the pressure history by observing the pressure loss during vacuum use and the actual pressure graph applied to the product. By observing the actual pressure applied in the cavity, the user can optimize the vacuum equipment selection and apply it to real life.
- See More
- Inclusion
- Oxide Prediction during Filling
- In general, Al alloy is used in the low pressure die casting process, and due to the characteristics of Al alloy, it is vulnerable to oxidation. Oxide is formed due to air contact with the free surface of melt during filling, and there is a high probability of defects occurring in areas where the formed oxide is concentrated.
- See More
- Microporosity
- Micro Shrinkage Defects using Gas Concentration
- This is a method of identifying shrinkage defect areas that are difficult to predict by the retained melt tracing method during solidification, which is a general shrinkage defect method, which is predicted by gas in the melt.
Microporosity calculations can consider external pressure. Using these points, microporosity is used when checking shrinkage defects in Counter Pressure Casting (CPC). - See More
- Cooling Channel
- Improved Analysis Accuracy by Channel
Consideration - It is possible to maintain the temperature balance of the mold, control shrinkage defects, and minimize deformation by using cooling and constant temperature channels during solidification. For special channels such as spot channel cooling, heat transfer coefficients according to the length of the channel are set to be similar to the actual product. The user may take into account the cooling effect.
- See More
- Improved Analysis Accuracy by Channel
- Speed
- Reduce Time Consuming Work
- Auto-Mesh creates meshes within 3-clicks for beginners. It detects the thickness of each area in the casting design, automatically adjusts the number of meshes, and generates meshes on the x, y, and z axis. In addition, it is possible to draft a report using the preset basic form through simple information input and observe the result like anyPOST in PowerPoint. Results Combination, which allows union and intersection combinations based on multiple results, enables various and clear result prediction.
- See More
Metal Mold Casting
Simulate Real Motions
such as Tilting and Rotation
What we can simulate in the
Metal Mold Casting process
Metal Mold Casting
Shrinkage
Prediction of Micro &
Macro Shrinkage Defect
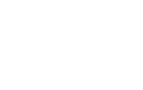
Analysis of Shrinkage from Solidification Pattern & Gas
The area of residual melt isolated during solidification is tracked to predict areas with high possibility of macro shrinkage defects based on the probabilistic defect model. Micro shrinkage – which are difficult to predict by tracking residual melt, can be predicted by considering the gas concentration inside the melt during solidification leading to observing the growth mechanism of gas.



Metal Mold Casting
Alloy
Shrinkage Prediction Accuracy
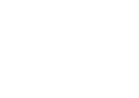
Thermal Properties Calculation
If there is no information to be used in the thermal property database within the program, the user can calculate the thermal property required for analysis by entering the chemical composition of the material. The thermal properties of a material are the most basic data in the analysis. In order to simulate accurately, the exact thermal data must be used.



Metal Mold Casting
Gas
Gas Porosity Defects

Core Gas Defect Before & After Filling
Gas Pressure is predicted by calculating the pressure of melt and isolated air area whereas Gas Amount predicts the movement, isolated distribution and amount of gas. It is possible to observe the movement of core gas generated from the contact in between the melt and the core along with the final isolated area. The results can then be expressed as a graph oh the amount of gas generated and discharged amount through the vent, etc.



Metal Mold Casting
Tilting
Easy Setting of
Casting Condition
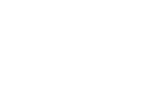
Gravity Tilting Pour Casting
In the gravity tilt casting, set the tilt axis and direction along with the center point when tilting and enter the angle according to the tilt time. The amount of melt in the hopper is automatically calculated and set within the program and the user can change it as well. Analysis from the melt pouring process in the hopper is also possible by modeling a separate gate on the upper surface of the hopper.



Metal Mold Casting
Microporosity
Shrinkage Induced
Gas Porosity (SIGAP)
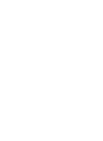
Determine Micro Shrinkage Defect with Gas Concentration
This is a method of identifying shrinkage defect areas that are difficult to predict by the observing the retained melt during solidification, which is generally used to identify defects by predicting gas in the melt. This method considers the growth of gas bubble in the molten metal during solidification, and is a method differentiated from other micro shrinkage defect prediction techniques.



Metal Mold Casting
Inclusion
Predict of Various Inclusions
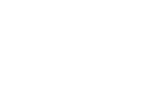
Oxide Prediction during Filling
Most of the inclusions in the gravity tilting pour casting and the centrifugal casting are oxides. In the case of gravity tilting pour casting, it is necessary to check whether the generated oxides move to the riser area. In case of centrifugal casting, it is important to know where the generated oxides are finally located due to rotation.



Metal Mold Casting
Centrifugal
Easy Setting of
Casting Condition
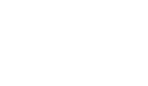
Centrifugal Casting
Centrifugal casting is divided into horizontal and vertical types, and in detail, it can be divided into injection at the rotation center axis and injection at out of the rotation center axis. Analysis setting for all conditions of centrifugal casting is possible, input rotation speed (rpm) for rotation, and information on rotation axis, direction, and rotation center point are essential.



Metal Mold Casting
Speed
Save Human Resource
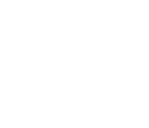
Reduce Time Consuming Work
Auto-Mesh creates meshes within 3-clicks for beginners. It detects the thickness of each area in the casting design, automatically adjusts the number of meshes, and generates meshes on the x, y, and z axis. In addition, it is possible to draft a report using the preset basic form through simple information input and observe the result like anyPOST in PowerPoint. Results Combination, which allows union and intersection combinations based on multiple results, enables various and clear result prediction.



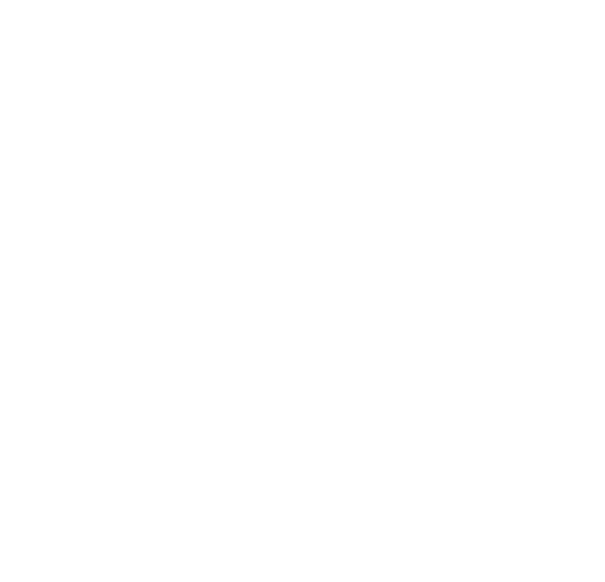
- Shrinkage
- Analysis of Shrinkage from Solidification Pattern & Gas
- The area of residual melt isolated during solidification is tracked to predict areas with high possibility of macro shrinkage defects based on the probabilistic defect model. Micro shrinkage – which are difficult to predict by tracking residual melt, can be predicted by considering the gas concentration inside the melt during solidification leading to observing the growth mechanism of gas.
- See More
- Alloy
- Thermal Properties Calculation
- If there is no information to be used in the thermal property database within the program, the user can calculate the thermal property required for analysis by entering the chemical composition of the material. The thermal properties of a material are the most basic data in the analysis. In order to simulate accurately, the exact thermal data must be used.
- See More
- Gas
- Core Gas Defect Before & After Filling
- Gas Pressure is predicted by calculating the pressure of melt and isolated air area whereas Gas Amount predicts the movement, isolated distribution and amount of gas. It is possible to observe the movement of core gas generated from the contact in between the melt and the core along with the final isolated area. The results can then be expressed as a graph oh the amount of gas generated and discharged amount through the vent, etc.
- See More
- Tilting
- Gravity Tilting Pour Casting
- In the gravity tilt casting, set the tilt axis and direction along with the center point when tilting and enter the angle according to the tilt time. The amount of melt in the hopper is automatically calculated and set within the program and the user can change it as well. Analysis from the melt pouring process in the hopper is also possible by modeling a separate gate on the upper surface of the hopper.
- See More
- Microporosity
- Determine Micro Shrinkage Defect with Gas Concentration
- This is a method of identifying shrinkage defect areas that are difficult to predict by the observing the retained melt during solidification, which is generally used to identify defects by predicting gas in the melt. This method considers the growth of gas bubble in the molten metal during solidification, and is a method differentiated from other micro shrinkage defect prediction techniques.
- See More
- Inclusion
- Oxide Prediction during Filling
- Most of the inclusions in the gravity tilting pour casting and the centrifugal casting are oxides. In the case of gravity tilting pour casting, it is necessary to check whether the generated oxides move to the riser area. In case of centrifugal casting, it is important to know where the generated oxides are finally located due to rotation.
- See More
- Centrifugal
- Centrifugal Casting
- Centrifugal casting is divided into horizontal and vertical types, and in detail, it can be divided into injection at the rotation center axis and injection at out of the rotation center axis. Analysis setting for all conditions of centrifugal casting is possible, input rotation speed (rpm) for rotation, and information on rotation axis, direction, and rotation center point are essential.
- See More
- Speed
- Reduce Time Consuming Work
- Auto-Mesh creates meshes within 3-clicks for beginners. It detects the thickness of each area in the casting design, automatically adjusts the number of meshes, and generates meshes on the x, y, and z axis. In addition, it is possible to draft a report using the preset basic form through simple information input and observe the result like anyPOST in PowerPoint. Results Combination, which allows union and intersection combinations based on multiple results, enables various and clear result prediction.
- See More
Investment Casting
Accurate Analysis
Considering the Effect of Radiation
What we can simulate in the
Investment Casting process
Investment Casting
Gas
Gas Porosity Defects

Gas Defect Occurrence During & After Filling
Gas Pressure is predicted by calculating the pressure of melt and isolated air area whereas Gas Amount predicts the movement, isolated distribution and amount of gas. It is possible to measure the gas amount by entity and measure specific areas by using additional modeling.



Investment Casting
Shell Heat Transfer
Heat Transfer in
Shell Surface & Atmosphere
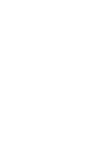
Consideration of Radiation
In the case of investment casting with a higher shell mold temperature compared to other casting processes, the radiation effect due to surrounding temperature must be considered. In other words, since accurate consideration of the air temperature around the shell mold must be made, the radiation effect is considered by modeling of air layer and adjusting heat transfer coefficient.



Investment Casting
Shrinkage
Prediction of Micro
& Macro Shrinkage Defect
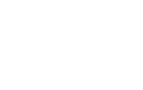
Analysis of Shrinkage from Solidification Pattern & Gas
The area of residual melt isolated during solidification is tracked to predict areas with high possibility of macro shrinkage defects based on the probabilistic defect model. Micro shrinkage – which are difficult to predict by tracking residual melt, can be predicted by considering the gas concentration inside the melt during solidification leading to observing the growth mechanism of gas.



Investment Casting
Microporosity
Prediction of Micro Shrinkage
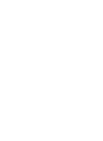
Micro Shrinkage Defect using Gas Concentration
This is a method of identifying shrinkage defect areas that are difficult to predict by the observing the retained melt during solidification, which is generally used to identify defects by predicting gas in the melt. This method considers the growth of gas bubble in the molten metal during solidification, and is a method differentiated from other micro shrinkage defect prediction techniques.



Investment Casting
Inclusion
Predict of Various Inclusions
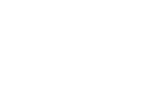
Oxide Prediction during Filling
Most of the common inclusion defects are oxides generated during filling and the generated oxides are distributed in the gate area that functions as a riser. However, in screw-shaped products such as propellers, oxides are concentrated in the blade area causing problems, so oxide analysis is also one of the important prediction results.



Investment Casting
Management
Assemble Runner &
Gate Designs
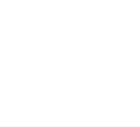
Increasing Productivity
When multiple products are produced in a single casting design, differences in soundness between each product may occur due to product placement, runner shape, and ingate shape and placement. Through functions such as changing the modeling location before analysis and experience over a long period of time, AnyCasting derives and presents the optimal plan for productivity improvement.



Investment Casting
Speed
Save Human Resource
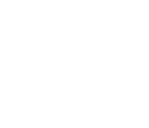
Reduce Time Consuming Work
Auto-Mesh creates meshes within 3-clicks for beginners. It detects the thickness of each area in the casting design, automatically adjusts the number of meshes, and generates meshes on the x, y, and z axis. In addition, it is possible to draft a report using the preset basic form through simple information input and observe the result like anyPOST in PowerPoint. Results Combination, which allows union and intersection combinations based on multiple results, enables various and clear result prediction.



Investment Casting
Alloy
Thermo Dynamics Calculation
of Material Properties
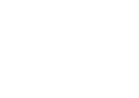
Thermal Properties Calculation
If there is no information to be used in the thermal property database within the program, the user can calculate the thermal property required for analysis by entering the chemical composition of the material. The thermal properties of a material are the most basic data in the analysis. In order to simulate accurately, the exact thermal data must be used.




- Gas
- Gas Defect Occurrence During & After Filling
- Gas Pressure is predicted by calculating the pressure of melt and isolated air area whereas Gas Amount predicts the movement, isolated distribution and amount of gas. It is possible to measure the gas amount by entity and measure specific areas by using additional modeling.
- See More
- Shell Heat Transfer
- Consideration of Radiation
- In the case of investment casting with a higher shell mold temperature compared to other casting processes, the radiation effect due to surrounding temperature must be considered. In other words, since accurate consideration of the air temperature around the shell mold must be made, the radiation effect is considered by modeling of air layer and adjusting heat transfer coefficient.
- See More
- Shrinkage
- Analysis of Shrinkage from Solidification Pattern & Gas
- The area of residual melt isolated during solidification is tracked to predict areas with high possibility of macro shrinkage defects based on the probabilistic defect model. Micro shrinkage – which are difficult to predict by tracking residual melt, can be predicted by considering the gas concentration inside the melt during solidification leading to observing the growth mechanism of gas.
- See More
- Microporosity
- Micro Shrinkage Defect using Gas Concentration
- This is a method of identifying shrinkage defect areas that are difficult to predict by the observing the retained melt during solidification, which is generally used to identify defects by predicting gas in the melt. This method considers the growth of gas bubble in the molten metal during solidification, and is a method differentiated from other micro shrinkage defect prediction techniques.
- See More
- Inclusion
- Oxide Prediction during Filling
- Most of the common inclusion defects are oxides generated during filling and the generated oxides are distributed in the gate area that functions as a riser. However, in screw-shaped products such as propellers, oxides are concentrated in the blade area causing problems, so oxide analysis is also one of the important prediction results.
- See More
- Management
- Increasing Productivity
- When multiple products are produced in a single casting design, differences in soundness between each product may occur due to product placement, runner shape, and ingate shape and placement. Through functions such as changing the modeling location before analysis and experience over a long period of time, AnyCasting derives and presents the optimal plan for productivity improvement.
- See More
- Speed
- Reduce Time Consuming Work
- Auto-Mesh creates meshes within 3-clicks for beginners. It detects the thickness of each area in the casting design, automatically adjusts the number of meshes, and generates meshes on the x, y, and z axis. In addition, it is possible to draft a report using the preset basic form through simple information input and observe the result like anyPOST in PowerPoint. Results Combination, which allows union and intersection combinations based on multiple results, enables various and clear result prediction.
- See More
- Alloy
- Thermal Properties Calculation
- If there is no information to be used in the thermal property database within the program, the user can calculate the thermal property required for analysis by entering the chemical composition of the material. The thermal properties of a material are the most basic data in the analysis. In order to simulate accurately, the exact thermal data must be used.
- See More
Large Ingot Casting
Accurate Defect Prediction
Experience of Various Tonnage Product
What we can simulate in the
Large Ingot Casting process
Large Ingot Casting
Shrinkage
Prediction of
Shrinkage Defect
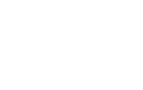
Shrinkage Defect due to Solidification Pattern
The area of melt that is isolated upon solidification is tracked to determine the shrinkage defect area using a probabilistic defect parameter technique. In the case of ingot casting, it is possible to predict micro-shrinkage in consideration of temperature gradient and to predict the cracking area inside of product using hot tearing intensity.



Large Ingot Casting
Alloy
Shrinkage Prediction
Accuracy
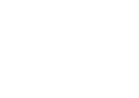
Thermal Properties Calculation
If there is no information to be used in the thermal property database within the program, the user can calculate the thermal property required for analysis by entering the chemical composition of the material. The thermal properties of a material are the most basic data in the analysis. In order to simulate accurately, the exact thermal data must be used.



Large Ingot Casting
Segregation
Segregation Considering
Natural Convection
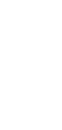
Segregation Distribution Prediction
Among the defects occurring in ingot casting, segregation defects are one of the most important predictions to be made. The natural convection that occurs inside the product during solidification must also be considered. Based on the user input value, the difference in concentration are calculated to show the results which predict A segregation, V segregation, inverse segregation and negative segregation.



Large Ingot Casting
Exothermic
Enhance Feeding of Riser
by Exothermic Powder
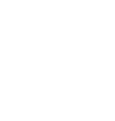
Prediction of Defects by Exothermic effect
In order to maximize the feeding effect of the riser, whether it is possible to consider the effect of the exothermic powder applied to the top of riser after filling is very important in the ingot casting analysis. It is possible to control defects generated in the product depending on the use of the exothermic powder and the performance of the exothermic powder.



Large Ingot Casting
Additional Pouring
The Effect of
Additional Pouring
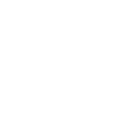
Effect of Additional Pouring
Due to the nature of the ingot casting process, it is not possible to completely fill the mold with a single pour, so there must be additional pouring. It is crucial to consider the internal temperature and segregation that changes due to additional pouring and often intended to induce directional solidification.



Large Ingot Casting
Inclusion
Tracing Inclusions
during Filling
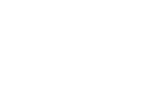
Gas, Oxide & Slag
It is possible to check the behavior of gas and oxide & slag generated during filling and the final isolation location. These defects are harmful to the soundness of the ingot product and must be considered when checking the results of the filling analysis, through the quantitative analysis function, the amount of isolated gas in a specific area can be identified and the amount of isolation for each plan can be checked.



Large Ingot Casting
Management
Design for Large Ingot Casting
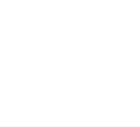
Increasing Productivity
In the ingot casting process, gating design and mold design come from experience of each manufacturer and are the factors that have a significant influence on the soundness of a product. Based on years of analysis experience using AnyCasting, optimizing the soundness of ingot products is presented and analytically verified.



Large Ingot Casting
Speed
Save Human Resource
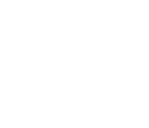
Reduce Time Consuming Work
Due to the size of the product, the ingot casting process takes a long time to filling and solidification. Time loss occurs in the simulation. AnyCasting ingot casting analysis method provides a fast ingot solver function to minimize time loss, dramatically reducing the analysis time during filling.
This is the effect of reducing the analysis time by more than 2 times as much as the general analysis time.



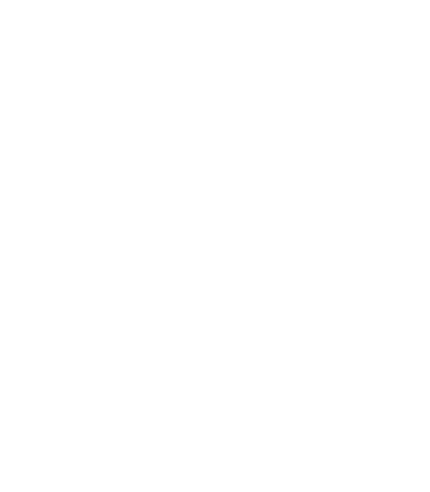
- Shrinkage
- Shrinkage Defect due to Solidification Pattern
- The area of melt that is isolated upon solidification is tracked to determine the shrinkage defect area using a probabilistic defect parameter technique. In the case of ingot casting, it is possible to predict micro-shrinkage in consideration of temperature gradient and to predict the cracking area inside of product using hot tearing intensity.
- See More
- Alloy
- Thermal Properties Calculation
- If there is no information to be used in the thermal property database within the program, the user can calculate the thermal property required for analysis by entering the chemical composition of the material. The thermal properties of a material are the most basic data in the analysis. In order to simulate accurately, the exact thermal data must be used.
- See More
- Segregation
- Segregation Distribution Prediction
- Among the defects occurring in ingot casting, segregation defects are one of the most important predictions to be made. The natural convection that occurs inside the product during solidification must also be considered. Based on the user input value, the difference in concentration are calculated to show the results which predict A segregation, V segregation, inverse segregation and negative segregation.
- See More
- Exothermic
- Prediction of Defects by Exothermic effect
- In order to maximize the feeding effect of the riser, whether it is possible to consider the effect of the exothermic powder applied to the top of riser after filling is very important in the ingot casting analysis. It is possible to control defects generated in the product depending on the use of the exothermic powder and the performance of the exothermic powder.
- See More
- Additional Pouring
- Effect of Additional Pouring
- Due to the nature of the ingot casting process, it is not possible to completely fill the mold with a single pour, so there must be additional pouring. It is crucial to consider the internal temperature and segregation that changes due to additional pouring and often intended to induce directional solidification.
- See More
- Inclusion
- Gas, Oxide & Slag
- It is possible to check the behavior of gas and oxide & slag generated during filling and the final isolation location. These defects are harmful to the soundness of the ingot product and must be considered when checking the results of the filling analysis, through the quantitative analysis function, the amount of isolated gas in a specific area can be identified and the amount of isolation for each plan can be checked.
- See More
- Management
- Increasing Productivity
- In the ingot casting process, gating design and mold design come from experience of each manufacturer and are the factors that have a significant influence on the soundness of a product. Based on years of analysis experience using AnyCasting, optimizing the soundness of ingot products is presented and analytically verified.
- See More
- Speed
- Reduce Time Consuming Work
- Due to the size of the product, the ingot casting process takes a long time to filling and solidification. Time loss occurs in the simulation. AnyCasting ingot casting analysis method provides a fast ingot solver function to minimize time loss, dramatically reducing the analysis time during filling.
This is the effect of reducing the analysis time by more than 2 times as much as the general analysis time. - See More
Click Process and see more details
News & Events
Meet the Latest
News & Events
from AnyCasting!
AnyCasting will pursue sustaining
its growth by creating high values
through innovations

AnyCasting S/W Exceeded
700+ Users, Globally
Join This party & Contact Us.
Global Partners
Partnership with AnyCasting Software,
In Europe, Asia, North America
Collaborations
Ohio State UniversityTechnical Co-work
Ohio, USASMFACTechnical Co-work
Mexico
Collaborations
FondarexTechnical Co-work
SwissCPCTechnical Co-work
BulgariaAzterlanTechnical Co-work
Spain
Branch & Resellers
HeadquartersSeoul, Korea
Branch OfficeJinan, China
Overseas AgentTurkey
Taiwan
Thailand
India
China
Malaysia
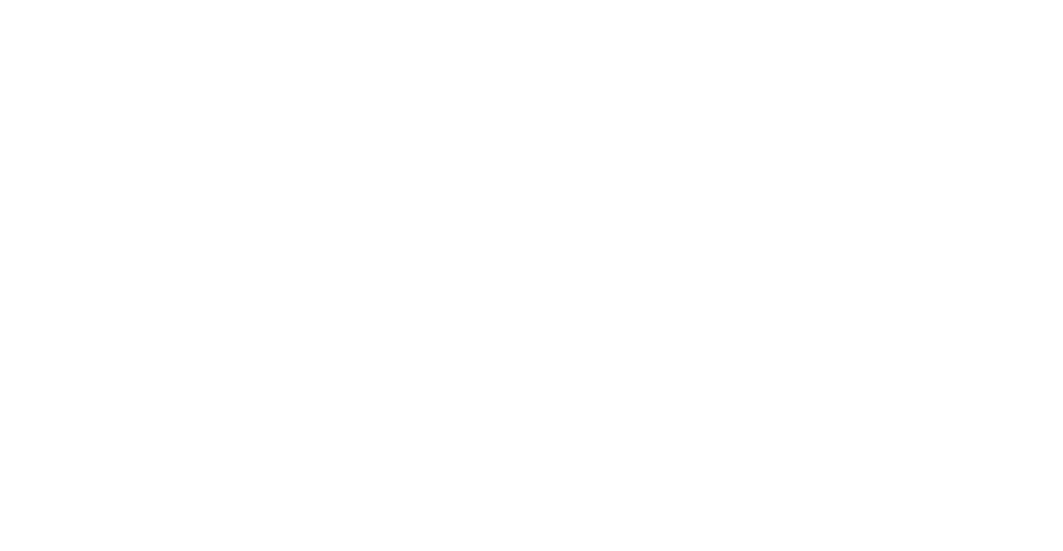
Company
History
-
2001
Founded
“AnyCasting Co. Ltd.,” -
2002
Expanded Business Internationally
-
2005
ISO 9001 & 14001,
INNO-BIZ Verified -
2006
Launched Branch Office
in China -
2010
Received
Prime Minister’s Award -
2014
Received
Presidential Award -
2015
Established
“AnyCasting Software Co. Ltd.,” -
2019
Received
Award from NADCA
21Years
History
-
2001Founded
“AnyCasting Co. Ltd.,” -
2002Expanded Business Internationally
-
2005ISO 9001 & 14001,
INNO-BIZ Verified -
2006Launched Branch Office
in China -
2010Received
Prime Minister’s Award -
2014Received
Presidential Award -
2015Established
“AnyCasting Software Co. Ltd.,” -
2019Received
Award from NADCA